T25KCB
Manufacturing Consultant and Executive Coach
Metal Processing

Production Manager
Project Length
-
12 Months
Objective
-
Maintain delivery to clients after company was brought out of administration
Issues to start with
-
Shop floor layout
-
Raw Material Identification & storage
-
Inventory Control
-
Production Planning
-
Labour Efficiency
Plan to fix it
-
Improve the shop floor layout to improve material flow & reduce waste.
-
Allocate fixed Locations for Material Storage.
-
Improve inventory control by implementing a Lot Tractability System on raw material.
-
Introduce Visual Management System for Production Planning
-
Implement a 3-shift system to reduce costs and improve key machine efficiencies.
Issues on the way
-
Negative Cashflow
-
Invoice Factoring Restrictions
Result
-
Managed to full fill all customer requirements and pay employee wages before Administrators were called in for a 2nd time.
Preventative Maintenance Programme
Project Length
-
12 Months
Objective
-
Reduce machine Downtime. Reduce H+S Issues near misses
Issues to start with
-
No preventative maintenance program in place
-
Repeated breakdowns on same equipment
-
No budget for TPM
-
High occurrence of near misses due to oil leaks
Plan to fix it
-
Carry out assessments on all Hydraulic Systems
-
Create action plan based on report
-
Introduce a TPM budget
-
Introduce a Preventative Maintenance Plan
-
Sub contract Quarterly and annual inspections and maintenance
Issues on the way
-
Reluctance to Change
-
Aged Work force
-
Long term illness in department
Result
-
Machine downtime reduced to less than 1%
-
Housekeeping dramatically improved
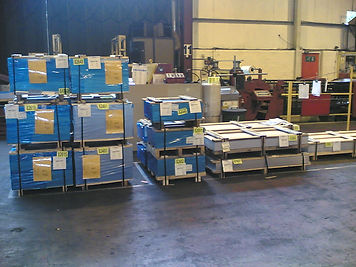
Material Flow Improvments
Project Length
-
12 months
Objective
-
Improve Material Flow from Goods Inwards to Customer
Issues to start with
-
No workshop organisation
-
Poor Raw and Finished Goods storage
-
Poor Delivery Performance
-
One off Special Deliveries
-
New pallets being procured for each shipment
-
No structure to return of pallets
-
Plan to fix it
-
Introduce 5S
-
Re laid out Materials Stores to improve space utilisation
-
Purchase a side loading FLT
-
Set up Standard pallets sizes & shop stocks at suppliers to be called off
-
Set up Shop Stocks of finished goods for Key Customers
-
Implement Fixed Slot Variable Batch (Tete Tete) production on Key Machines.
-
Implement and run Kanban system on slitting, Polishing & Blanking Lines
-
Implement JIT supply/collection system for Pallets from customers.
-
Organise backloads to collect pallets from Customers
-
Introduce Milk runs
Issues on the way
-
Explaining and implementing demand Pull with Suppliers & Customers
-
Setting up fixed slot variable batch Production.
-
Working with Transport company to improve vehicle Utilisation
Result
-
Improved productivity and enhanced DOTIF from 66% to 97%.
-
Reduced transport costs by 2%,
-
Reduced packaging costs by 88%
-
Eliminated aged stock